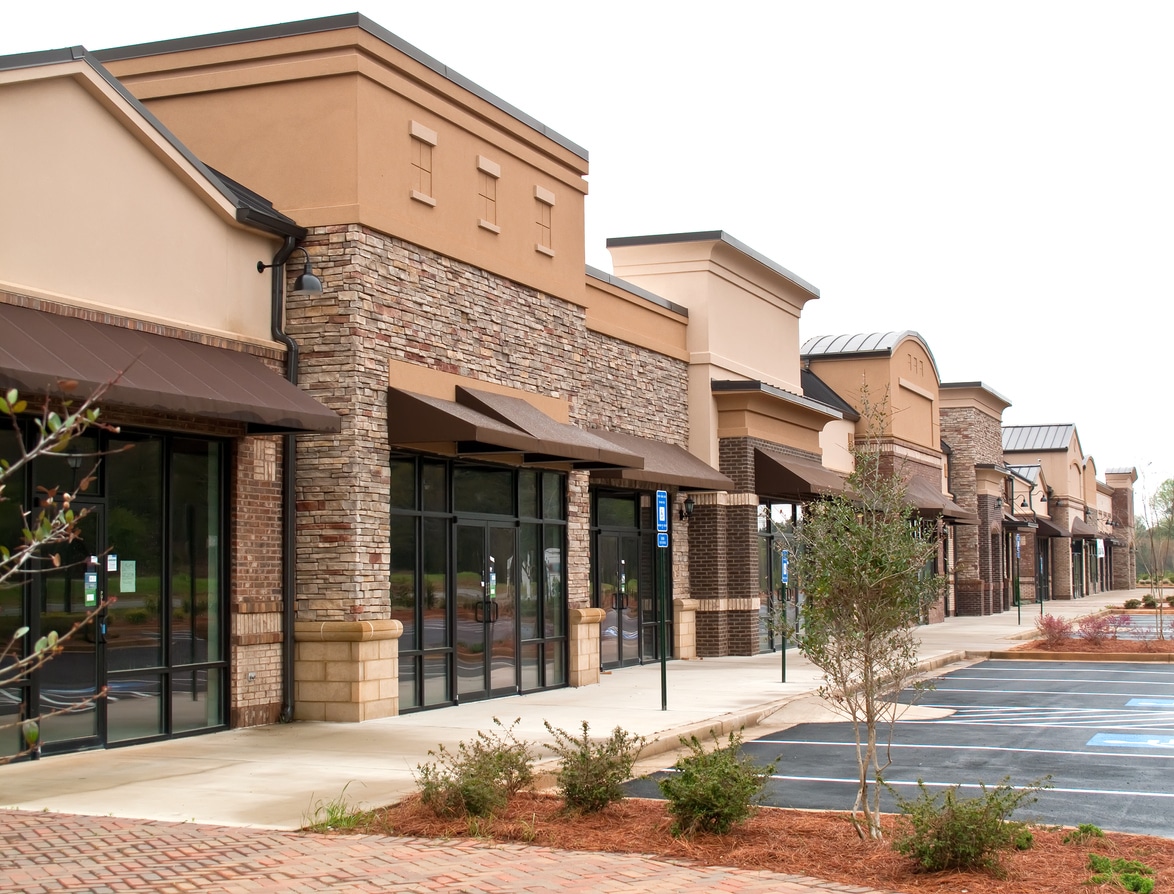
How Can Commercial Buildings Become More Sustainable?

For the past few decades, most sustainable advances in commercial real estate have been an afterthought. Construction professionals and architects use the same long-standing design methods. When businesses move into the buildings, some do their part to “greenify” the space, installing LED lights, installing solar panels and turning down the thermostat at the end of the night. These efforts, while possibly well-intentioned, are simply slapping a bandage on the underlying problem.
Operational vs. Embodied Carbon
Most companies adjust their operational carbon — emissions caused by the day-to-day running of their office. While it certainly makes sense to tackle these changes, it misses a significant chunk of the picture.
Many commercial structures fall short with embodied carbon, which begins long before a business moves in. Materials manufacturing, transportation and on-site practices all make up the embodied carbon, which is responsible for 50% of the whole-life carbon emissions in buildings.
Tips for More Sustainable Commercial Construction
It’s up to construction professionals and project managers to create buildings that minimize emissions from the start. These steps will set you on the right path to make your projects more sustainable now and for the long haul.
Shifting to Modular Construction
Typical on-site construction tends to have lax to non-existent sustainability standards — they burn through energy rapidly, use the most available materials and create tons of waste. These practices hurt the environment, but one slight shift could transform the industry.
Prefabricated or modular construction is on the rise as a much more efficient and sustainable building method. Factories can enforce strict standards and control emissions more carefully. Using prefabricated concrete molds produces considerably less carbon than pouring and casting on-site. These factories can also reuse materials between projects, drastically reducing construction waste.
You can design and order any size you need, from a room or two up to an entire commercial building. The modular design saves carbon emissions and drastically reduces project timelines, which will keep your clients happy.
Reusing Leftover Supplies
Construction and demolition (C&D) materials consist of the leftovers and debris from these projects. The U.S. alone produces around 600 tons a year, much of which sits in landfills contributing to further carbon emissions.
Professionals like you can stop the excess waste and reduce the environmental impact of construction and demolition processes. All it takes is some more practical use of leftover supplies.
Old doors and windows are easily repurposable since you can remove, repair and reinstall them at a new site. Lumber is another handy resource — cut it down to whatever size you need or use it as mulch. Glass, steel, concrete and other similar materials can be broken down and made new. You can recycle materials from past projects or buy C&D items from others. Either way, you’re doing your part to keep more out of landfills and reduce the global impact of your industry.
Creating Multi-Functional Buildings
You typically design commercial buildings for one function — either storage or offices. Companies needing both types of facilities must rent or purchase two spaces. As a result, extra carbon emissions come from building the additional structures and transportation between the multiple locations. The answer is to create multi-functional buildings or flex spaces.
These places look like warehouses with large open floor plans and high ceilings. The beauty is in the business owner’s imagination. They can use part of the building as a warehouse and section off a portion for office space. If they move out and another business takes over the building, it can transform to meet new needs. Flex spaces can also adapt and grow with a company, allowing them to reinvent their current space rather than expanding into a new build.
Repurposing Old Over Building New
Most commercial buildings aren’t designed to be as adaptable as a flex space. Designers intended them for one purpose — to suit the individual needs of their clients. Your opportunity moving forward is to repurpose those buildings into new usable spaces rather than choosing to construct an entirely new one.
A prime example of unused commercial real estate is the countless empty malls across the country. Their very presence is an environmental drain with no purpose. Tearing them down would create even more carbon emissions.
The best possibility is to revitalize these buildings and turn them into something more usable. Professionals like you are already reimagining these sites into hotels, event spaces, warehouses, churches, medical centers and so much more. The options are only as limited as your imagination.
Using Innovative Eco-Friendly Materials
A substantial portion of construction emissions originate in the choice of materials — cement manufacturing alone makes up 8% of total global emissions. Luckily, you’ll find quite a few sustainable alternatives on the market.
Bamboo and cork are fast-growing materials, only needing a few years to fully mature, which is a vast improvement over hardwoods. Both are beautiful and durable flooring options. They also weigh significantly less than other materials, so they cause fewer carbon emissions during transportation.
Insulation is another big sustainability issue for commercial buildings. Fortunately, you have many alternatives to traditional materials. Sheep’s wool is more expensive than some, but it’s biodegradable and naturally fire and mold-resistant. Another great option is plant-based polyurethane rigid foam. As the name suggests, this material is relatively immovable, so it works well for insulation. It’s also heat, pest and sound resistant.
The most significant contributor to construction emissions is concrete. You can go the prefabricated route, still using concrete but much more sustainably or use an alternate material. One of your best replacement options is ferrock, which is just as strong as traditional concrete but far better for the environment. Ferrock consists of recycled landfill scraps and industrial waste. It’s even carbon neutral or negative since its creation process pulls carbon from the air instead of releasing it.
Get to the Root of the Problem
Don’t settle for the same old designs and practices. Changing how you approach a construction project and address client requests will significantly impact your creation’s lifetime carbon emissions. Operational carbon can improve over time with the efforts of green-minded businesses.
However, embodied carbon is set from the beginning — you can’t go back later and change the effect of material production, transportation or on-site construction practices. The above measures are steps you can take right now to improve your process and make a real difference in protecting the environment.
Post a comment